The Theory Of Aluminum Die Casting
The Theory Of Aluminum Die Casting
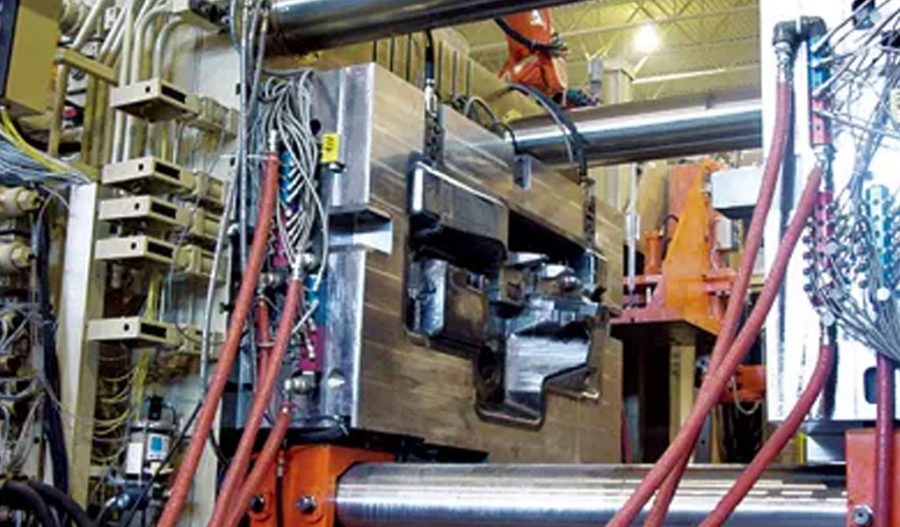
Aluminum alloy die-casting products are mainly used in electronics, automobiles, motors, home appliances and some communication industries. Some high-quality aluminum alloy thin wall die casting products with high performance, high precision and high toughness are also used in large aircraft, ships and other industries with relatively high requirements. . The main use is still on the parts of some instruments.
Casting aluminum alloy ingot production process: electrolytic aluminum liquid, waste aluminum ingot, scrap – batching – smelting tool preheating – slag removal in ladle – furnace loading – mixed smelting – furnace temperature control – slag removal and degassing – casting tool preheating ——Open the furnace hole to release molten aluminum – pouring – slag – cooling into indium – inspection – coding – packing – finished casting of aluminum alloy ingots.
Smelting operation: As described above, the pouring process is basically the same as that of ordinary casting, and the specific operations are related to the smelting of aluminum alloys and the casting of aluminum ingots for remelting.
It is mentioned in the die casting theory of aluminum die castings that continuous casting of horizontal ingot molds is the most commonly used casting method in aluminum electrolysis plants. Aluminium ingots for remelting of aluminium and aluminium alloys. A special volume die casting machine is used to realize this casting.
The horizontal continuous ingot casting method is a casting method with a high degree of mechanization of the block iron mold ingot casting method. The die casting mold technology is relatively simple. Because the aluminum alloy ingots for remelting are produced, the defects on the surface of the ingots and the requirements for the internal crystalline structure are relatively not strict. There are still requirements for pinhole grades inside the ingot. For the specific requirements of die casting ingots, please refer to the standard “Casting Aluminum Alloy Ingots”
Die Casting Process Control
The requirements for the process of horizontal continuous casting are mainly pouring temperature, pouring speed and water cooling control(The Theory Of Aluminum Die Casting).
- Pouring temperature The casting temperature of aluminum and aluminum alloy ingots for re-cultivation is different due to the different alloy varieties. In general, the pouring temperature of common aluminum and deformed aluminum alloys is in the range of 30-80 degrees above the crystallization temperature of the alloy. Cast aluminum alloys are in the range of 30 – 50 degrees above the crystallization temperature.
- Pouring speed Horizontal ingot mold continuous casting is a fixed casting machine. Different types of casting machines have different casting speeds. The casting speed is adjustable, and the casting speed is expressed by the travel speed of the mold. But to be more intuitive, foundries generally test casting speed by casting several ingots per minute. It should be emphasized that the casting speed should not be adjusted too fast, otherwise, it may cause the die casting machine to vibrate greatly, and the ingot will have serious ripples and surface oxidation.
- Cooling control The cooling method of the horizontal ingot mold continuous casting machine is divided into two types: one is the forced water-cooling type immersed at the bottom of the casting mold, which mainly controls the inlet water temperature to be below 40 degrees and the return water temperature to be below 60 degrees. The other is the natural cooling method of the ingot, but in order to ensure the normal operation of the casting machine, it is necessary to reduce the temperature of the casting mold, and spray cooling with water before or after the demoulding of the ingot, so as to reduce the temperature of the casting mold, that is, to avoid die casting mold cost.The equipment failure that may occur in the high temperature operation of the casting machine is also conducive to the demolding of the ingot and the stability of the process conditions. This cooling method generally requires the water spray temperature to be below 40 degrees.
Which Metal Should You Choose For Die Casting?
Which Metal Should You Choose For Die Casting?
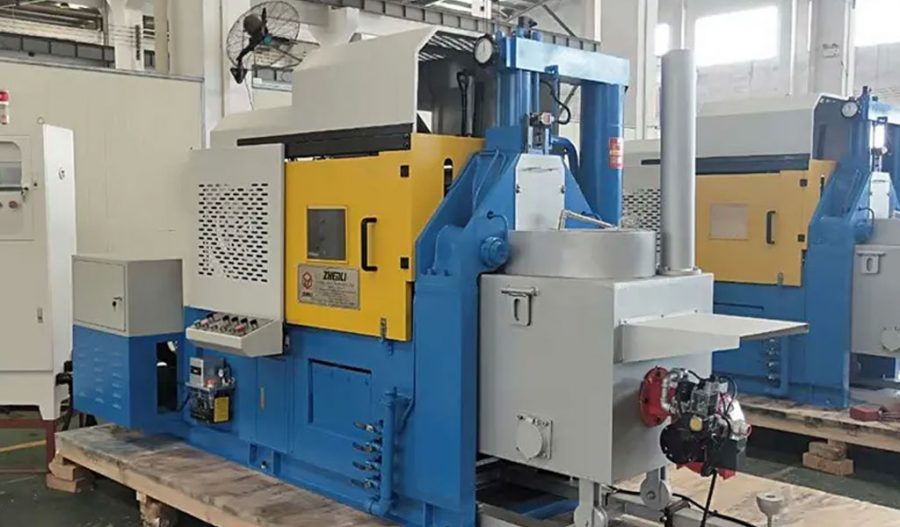
If you’re designing volume die casting of a part or product, choose a manufacturing process that can build it using the same material. In metal die casting, you can consider the process of cold chamber die casting process, which can build parts from different metal materials one layer at a time. Cold chamber die casting services is a injection chamber and the injection punch are not immersed in the molten metal, but a quantitative amount of molten metal is poured into the injection chamber and then injected. ,. This way, it can create highly complex shapes when other manufacturing methods can’t.
However, you need to know the best metals that can be used for your display die casting or other project. Choosing the correct metal will ensure optimum results and an effective die casting process that will improve your chances of success.
Which metals can be used in die casting?
Which Metal Should You Choose For Die Casting?Reputable manufacturers offer a range of materials, such as aluminum, zinc, copper, and magneium. These metals come with various properties, making them ideal for a range of applications. For instance, if you require volume production of automotive parts, pipes, or valves; aluminum and aluminum alloy can be a good option for offering outstanding corrosion resistance.
Metals to avoid in die casting
Any metal may be used in die casting if it can be supplied as an appropriate metal. However, materials that burn instead of melt at high temperatures should be avoided as they cannot be melted safely or sintered. Metals to avoid in die casting:
- Stainless Steel
- Titanium
- Greek Ascoloy.
- Carp 49
- Hastelloy
- Nitronic-60
- Inconel
- Hymu 80
- More
Benefits of Die Casting with High Volume
High Volume Thin Wall Die Casting and cnc machining is a versatile metal manufacturing technology that lets you build functional metal rapid prototypes and parts with complex shapes or geometries. It’s used extensively in the medical, automotive, and aerospace industries for fulfilling part consolidation and weight-saving application requirements. Creating prototypes and low-volume end-use parts out of Thin Wall Die Casting metals are typically detailed but not necessarily structurally sound.
Key Elements to Consider Before Proceeding with Die Casting
Key Elements to Consider Before Proceeding with Die Casting
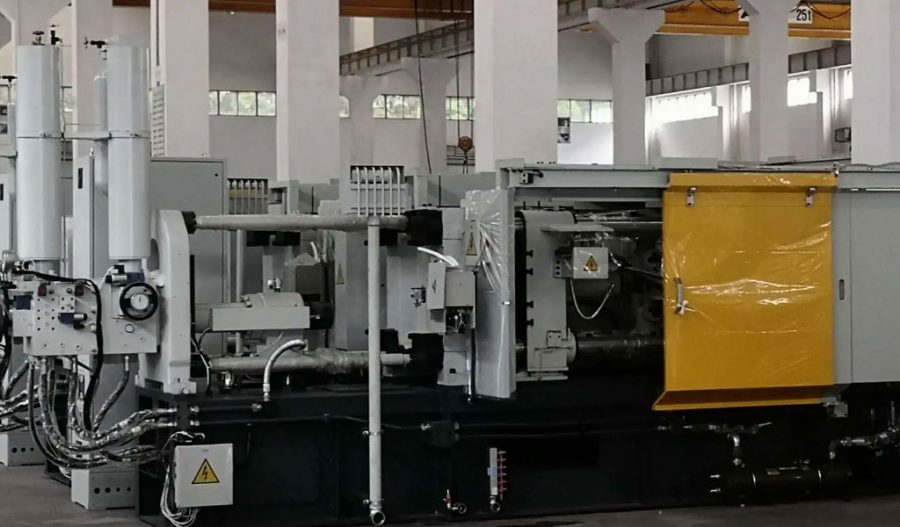
Getting your product from the drawing to a tangible version is a crucial aspect of design. Without it, you have no way to test and validate your design before it’s finalized for mass production. Die casting is one of the ways you can bring your designs to life. It involves die casting – molds manufacturing – CNC machining, which delivers high precision, fast, and durable prototypes of parts from a billet or block of your chosen material that is cut with a series of drill bits and tools.
Are you considering die casting for your project? Be sure to consider these Key Elements to Consider Before Proceeding before you proceed:
Die Casting Materials
Die casting allows you to volume make your model with almost all kinds of materials that can withstand heat and stress. Some of the most popular materials used are aluminum, zinc, and special alloy like magneium and copper.
Die Casting Machining methods
Die casting uses the cavity of the mold to apply high pressure to the molten metal. Molds are usually machined from stronger alloys, a process somewhat similar to injection molding.
Your Die Casting project
Die casting is used typically for volume building high-quality prototypes for functional testing. However, it’s also practical for crafting custom casts or molds to build prototypes for other production processes, such as injection molding. In this case, the CNC machining prototyping process also qualifies as rapid tooling.
Die Casting Tolerances
CNC machines can be very accurate, but running the mill on the highest accuracy can be time-intensive and costly. That’s why tolerances are used, and these are measurements indicating the level of precision required for the prototype you’re making. In short, they represent the degree of variation permitted in the measured value or final dimensions of the part. Reputable providers of CNC prototyping and edm wire cutting services control their tolerances to DIN-2678-1 Medium for Fine for metals.
Top 5 Advantages Of A CNC Machining Die Casting Parts Services
Top 5 Advantages Of A CNC Machining Die Casting Parts Services
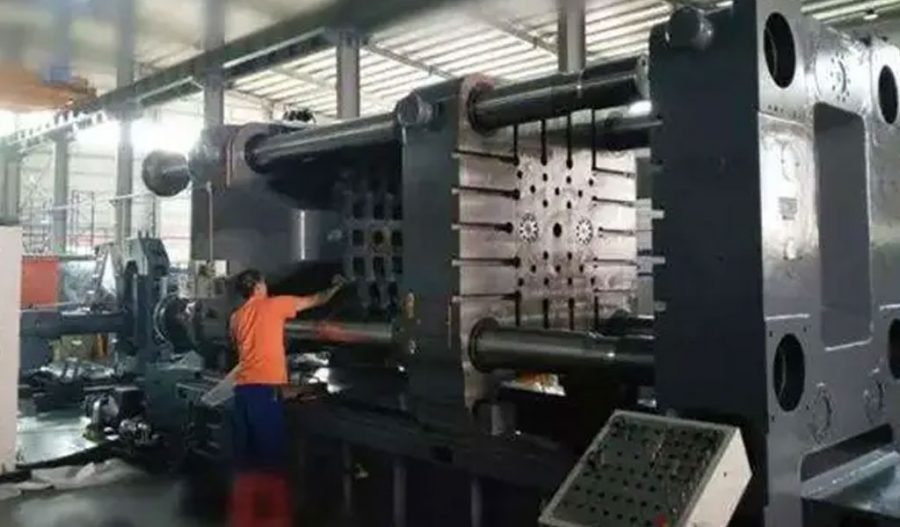
High Volume Manufacturing Parts test of your design is a must as it allows you to test your die casting product(as lighting die casting parts) and refine your ideas. That makes it an important aspect of the product development process. While it can be expensive and time-consuming, you have the option to outsource it to a reputable CNC Machining service. Thus, you can focus on other areas of your project and ensure the speedy and accurate creation of an aesthetic or functional model for your design.
During Precision Machining, your research and development team can identify and validate promising concepts based on the design samples. A prototype allows them to test the design’s core features with users to have a clearer idea of how the concept can meet the market demand. It also lets them make the necessary adjustments to the design before it goes into final production.
Here are more top advantages of CNC Machining die casting parts services:
Reduce product development expenses
The CNC Machining service eliminates the need to purchase your die casting molding material and manufacturing devices. This way, you can save time and money while ensuring that your final product can be realized faster and cost-effectively, with better ROI.
Avoid product failure
The service provider can ensure accurate and precise manufacturing of your CNC Machining samples based on your exact design. This way, product designers can identify any flaws and make corrections or improvements. Moreover, it ensures a more ergonomic way to identify and evaluate product hazards.
Functionality testing
The CNC Machining samples shows the exact function and aesthetics of your product.CNC Machining and Surface Treatment services will ensure speedy results so you can test and retest quickly and find ways to fine-tune your ideas.
Access to more technologies
A reputable rapid cnc prototype machining service offers a range of technologies and solutions to create functional or aesthetic products. These include Metal 3D printing, vacuum casting, injection molding, and CNC machining.
Make sound decisions
Established providers of cnc machining services in China can review your project for free. It’s a great chance to learn how they can help you, especially if you’re unsure which die casting methods are best for your design.
Things to Consider While Getting Online Die Casting Services
Things to Consider While Getting Online Die Casting Services
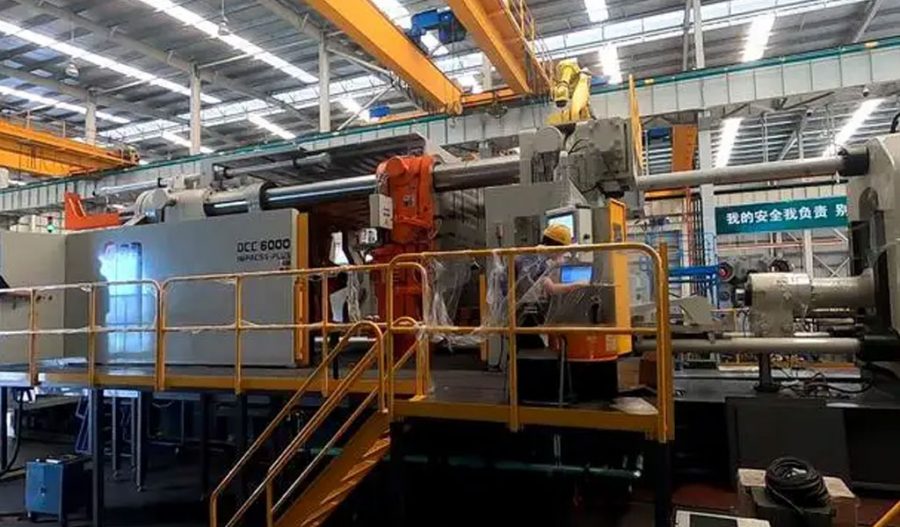
Some product manufacturers may be looking for a better die casting company, while others are new to outsourcing the service to a third party. No matter your situation, you require a dependable provider of online die casting services that can deliver high-precision parts fast. While there’s no shortage of options online, you may find it hard to choose the most suitable service provider. After all, your choice could mean the difference between your project’s failure and success. We’ll share the things you must consider to increase your chances of hiring the best die casting service provider online:
Online Die Casting Experience
Look for a die casting company or manufacturer with at least ten years of experience in providing online die casting services. Consider their experience in your industry, too. You could gauge their capabilities by exploring case studies and reading the customer testimonials. Just remember to take the latter with a grain of salt.
Online Die Casting Equipment
An online die casting service must have the right equipment to take on any project. Know the systems and technologies they use, such as surface grinding machines, sink and wire EDMs, lathes, and CNC mills. See if they have three, four, or five-axis machines, too. Reputable companies usually share them on their website to assist you make an informed choice to hire them. To ensure timely delivery, determine the number of die casting systems they have to ensure they have enough to accomplish your project on time.
Online Die Casting Standards
Ensure tight tolerances for die casting services. Reputable companies control tolerances to DIN-2768-1 Fine for metals and Medium for plastics as the standard.
Online Die Casting Certifications
Established online precision metal die casting services are accredited and certified by relevant entities, like ISO and IATF. Be sure they operate an ISO 9001 QMS qualified facility, and adhere to ISO 9001:2015 requirements. Competent service providers can also provide quality assurance reports and material certifications.
Online Die Casting Project review
Some online die casting services can review your project for free to help you plan accordingly. They can provide tips for designing your product(as medical die casting parts) and recommend other applicable services if required.
Tips for Finding the Best China Die Casting Parts Manufacturer
Tips for Finding the Best China Die Casting Parts Manufacturer
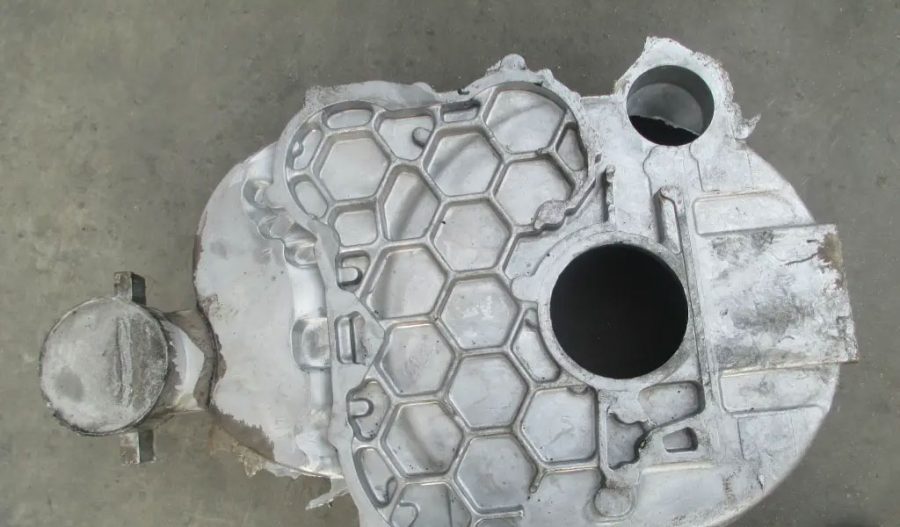
Are you looking in China for a die casting parts manufacturer? You might be overwhelmed by the many available options, especially when finding which china die casting company is dependable and trustworthy. The last thing you want to receive low-quality results that can waste your time and money and compromise the safety of your end product. To save you from the guesswork, we put together some tips to help you find the best die casting service and parts manufacturer in China.
Narrow down the options
Choose a China die casting parts manufacturer with extensive experience in volume end-use manufacturing. The company must be IATF 16949:2016, ISO 14001, and ISO 9001:2015 certified. It should have a multilingual team of experts that speaks your language, so the language barrier will be the least of your worries when collaborating with them.
Discuss your needs with Die Casting manufacturer
Consider your timeline and ensure the manufacturer can finish and deliver your project within the agreed period. Reputable die casting services can review your project for free to understand your requirements and make recommendations that may help reduce the costs and speed up the completion of your project.
Verify their Die Casting process and technologies
Find out the tolerances used by the China die casting parts manufacturer for metal and plastics. Reputable manufacturers control tolerances to DIN-2678-1 Medium for plastics and Fine for metals. They have a good selection of high-precision mills, die casting machine,sink and wire EDMs, lathes, axis machines, surface treatment and grinding machines, and other equipment to ensure the timely delivery of custom die casting parts. The manufacturing process should include a thorough quality check.
Verify their Die Casting experience
Check their case studies and explore customer testimonials. These can help determine if they have worked on projects similar to yours. Remember not to take the reviews at face value.
Ensure reliable customer service
Consider a China die casting parts manufacturer that maintains open communication with its clients. They should update you on your project’s progress and promptly inform you of important matters.
알루미늄 합금 다이캐스팅의 단점을 해결하는 것이 편리합니다!
알루미늄 합금 다이캐스팅은 현재 현재의 전자제품, 자동차, 생활필수품 등 많은 산업과 분야에서 널리 사용되고 있습니다. 그러나 알루미늄 합금 다이캐스팅에서 자주 발생하는 몇 가지 결함 및 해결 방법은 다음과 같습니다.
- 불순물
알루미늄 합금 다이 캐스팅의 불순물 문제는 주로 특정 온도에서 알루미늄, 규소 및 다량의 철, 망간, 크롬 및 기타 화합물을 포함하는 결정립과 일부 산화물로 구성됩니다.
해결책: 알루미늄 잉곳의 조성을 엄격하게 제어하고, 제련로의 난로를 정기적으로 청소하고, 정기적으로 슬래그를 처리하면 문제를 해결할 수 있습니다.
- 구강 문제
다공성은 다이캐스팅 부품의 내부 또는 표면에 나타나는 다양한 크기의 구멍을 말하며, 이는 다이캐스팅 부품의 경도 부족으로 이어져 표면의 외관에 영향을 줍니다.
Solution: 적절한 정제제를 사용하여 모공을 처리하고, 공정을 조정하고, 저속을 적절하게 줄이고, 이형제가 너무 많이 분사되어 모공 문제가 해결되지 않는지 확인하십시오.
- 균열 문제
균열은 알루미늄 합금 다이캐스팅의 매트릭스가 파괴되고, 외력의 작용에 따라 확장되는 경향이 있는 선형 또는 기타 라인인 기다란 틈이 형성되는 것을 의미합니다.
솔루션: 합금 조성을 올바르게 제어하고, 냉각수 회로를 늘리고, 알루미늄 합금 다이캐스팅의 구조를 변경하고, 사출 위치를 변경하거나 증가시키면 해결할 수 있습니다.
PINJIN서비스에는 다음이 포함됩니다. 알루미늄 다이캐스팅,아연 다이캐스팅,마그네슘 다이캐스팅,투자 주조,모래 주조,분실된 거품 주조,CNC 밀링,CNC 터닝,5축 CNC 가공,정밀 가공,신속한 프로토 타입,와이어 방전가공
저작권 고지: 이 기사의 출처는https://castingsmachining.com/