Application of DC cooling fan in various fields
Application of DC cooling fan in various fields
Cooling fans are generally used in printers, fax machines, banner machines, medical equipment, automotive electronics, power equipment, electric vehicle chargers, communication/communication cabinets, frequency converters, transformers, industrial control equipment, stage lighting (light source cooling), new energy ( Cooling fans are required for equipment such as batteries into cabinets), engine cooling, instruments and meters.
DC cooling fans have a wide range of applications, but cooling fans are generally installed inside the machine. Now, most devices will generate heat after running, and they need cooling fans to dissipate heat. The application of cooling fans in various fields is described in detail below.
Cooling fans are generally used in printers, fax machines, banner machines, medical equipment, automotive electronics, power equipment, electric vehicle chargers, communication/communication cabinets, frequency converters, transformers, industrial control equipment, stage lighting (light source cooling), new energy ( Cooling fans are required for equipment such as batteries into cabinets), engine cooling, instruments and meters.
The following is an example of the application of automobile cooling fans in automobiles
The replacement of automobiles clearly marks the changes of this era, and each generation of changes has higher and higher requirements for heat dissipation. From the initial heat dissipation, to the need to reduce noise while satisfying heat dissipation, and then to develop, not only reduce noise and heat dissipation, but also need to be able to control heat dissipation in real time, that is, to support PWM intelligence fan speed regulation cooling fans.
- During the operation of the car, heat is continuously generated, and the components around the combustion chamber (cylinder liners, cylinder heads, valves, etc.) must be properly cooled. The automobile cooling system is composed of radiator, thermostat, water pump, Communications,cylinder water channel, cylinder head water channel, fan, etc. The radiator is responsible for th,e cooling of circulating water. Its water pipes and heat sinks are mostly made of aluminum materials. The aluminum water pipes are made of flat shape, and the heat sinks are corrugated. The heat dissipation performance should be taken into account. The installation direction is perpendicular to the air activity direction. It is possible to achieve smaller wind resistance and higher cooling efficiency.
The coolant flows inside the radiator core and the air passes outside the radiator core. The hot coolant is cooled by dissipating heat to the air, and the cold air is warmed by receiving heat from the coolant, so the radiator is a heat exchanger. The cooling fan is installed in the radiator to blow away the heat in time to achieve the whole cooling effect.
our services include:dc-cooling-fan, centrifugal-fan, ac-cooling-fan, dc-blower, small-cooling-fan ,chip-coolers,computer-heatsink, aluminum-cpu-heat-sink, copper-cpu-heatsink, aluminum profile-heatsink
Copyright Notice: The source of this article is https://cpuheatsink.com/
The difference between the cooling fan ball bearing
The difference between the cooling fan ball bearing
The cooling fan has single ball and double ball bearings, which can be selected according to different needs. The following will introduce the difference between the two bearings.
single ball bearing
The single ball bearing adopts the form of sliding friction and ball friction. One ball bearing and oil-impregnated bearing are used to reduce the cost of the double ball bearing. The rotor and the stator are lubricated with balls, and lubricating oil is added. The service life is about 30,000-40,000 hours. .
Advantages: longer life than oil-impregnated bearings, stable operation, low cost
Disadvantages: Although the noise is small, the noise will increase for a long time
Double ball bearing
The double ball bearing is a high-end bearing. It adopts the form of rolling friction. There are two balls. The bearing has several tiny steel balls around the axis. When the fan blade or the axis rotates, the steel balls rotate along with it. Because it is a sphere, the friction force will be reduced. It is relatively small, and will not leak oil. It has a long service life and a service life of about 50,000-70,000 hours. It has good performance, high speed and large air volume.
Advantages: good sealing performance, long service life
Disadvantage: high cost
our services include:dc-cooling-fan, centrifugal-fan, ac-cooling-fan, dc-blower, small-cooling-fan ,chip-coolers,computer-heatsink, aluminum-cpu-heat-sink, copper-cpu-heatsink, aluminum profile-heatsink
Copyright Notice: The source of this article is https://cpuheatsink.com/
The difference between the cooling fan ball bearing
The difference between the cooling fan ball bearing
The cooling fan has single ball and double ball bearings, which can be selected according to different needs. The following will introduce the difference between the two bearings.
single ball bearing
The single ball bearing adopts the form of sliding friction and ball friction. One ball bearing and oil-impregnated bearing are used to reduce the cost of the double ball bearing. The rotor and the stator are lubricated with balls, and lubricating oil is added. The service life is about 30,000-40,000 hours. .
Advantages: longer life than oil-impregnated bearings, stable operation, low cost
Disadvantages: Although the noise is small, the noise will increase for a long time
Double ball bearing
The double ball bearing is a high-end bearing. It adopts the form of rolling friction. There are two balls. The bearing has several tiny steel balls around the axis. When the fan blade or the axis rotates, the steel balls rotate along with it. Because it is a sphere, the friction force will be reduced. It is relatively small, and will not leak oil. It has a long service life and a service life of about 50,000-70,000 hours. It has good performance, high speed and large air volume.
Advantages: good sealing performance, long service life
Disadvantage: high cost
our services include:dc-cooling-fan, centrifugal-fan, ac-cooling-fan, dc-blower, small-cooling-fan ,chip-coolers,computer-heatsink, aluminum-cpu-heat-sink, copper-cpu-heatsink, aluminum profile-heatsink
Copyright Notice: The source of this article is https://cpuheatsink.com/
Precision CNC Machining Services in China
Precision CNC Machining Services in China
In the process of industrialization and modernization of the country, it is impossible not to mention the cnc machining industry. With the development of science and technology, cnc machining has been developed and more accurate. In China, the demand for cnc milling and cnc turning is very high, especially in Dongguan City, which has the leading speed of infrastructure development in the country. Today, be-cu.com would like to introduce to you our cnc machining service in Pintejin Group.
■
Precision CNC Machining Services in China
In the process of industrialization and modernization of the country, it is impossible not to mention the cnc machining industry. With the development of science and technology, cnc machining has been developed and more accurate. In China, the demand for cnc milling and cnc turning is very high, especially in Dongguan City, which has the leading speed of infrastructure development in the country. Today, be-cu.com would like to introduce to you our cnc machining service in Pintejin Group.
The Analysis Of China’s Automotive Die Casting Industry
The Analysis Of China’s Automotive Die Casting Industry
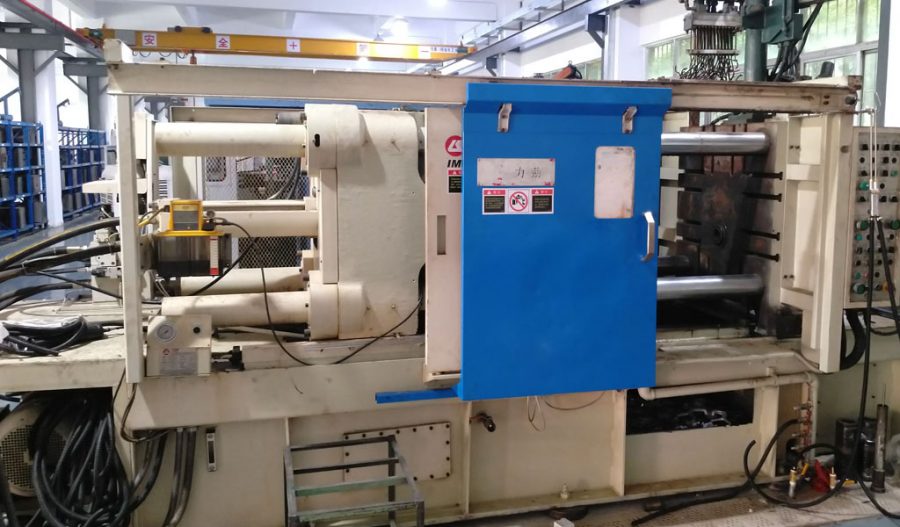
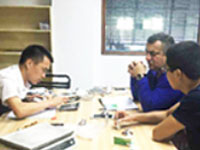
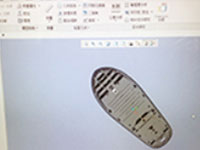
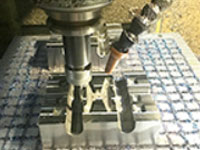
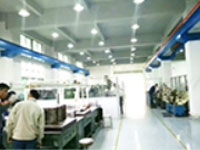
The metal materials used in die casting are mainly aluminum alloys, magnesium alloys, zinc alloys and copper alloys. Since aluminum alloy die castings are widely used in the automotive industry, they account for a high proportion of die castings. According to the statistics of China Foundry Association, the proportion of aluminum alloy die castings in die castings is about 85%.
Market overview of die casting industry
(1) Overview of the international market
In recent years, with the development of the global economy, the demand for precision die castings in many fields such as automobiles, 3C products, communication infrastructure equipment, household appliances, and medical equipment has steadily increased.
At present, the market maturity of die casting parts in developed countries is relatively high. With the improvement of die casting equipment and process technology, more and more ferrous metal castings are replaced by non-ferrous metal die castings such as aluminum alloy and magnesium alloy. The production and consumption of global die castings are mainly concentrated in the United States, China, Italy, Germany, Mexico, Japan and other countries.
For developed countries, due to their leading advantages in equipment and technology, china automotive die-casting industry is generally dominated by high-quality and high-value-added die-casting such as automobiles, communications, and aviation.
The number of die-casting enterprises in developed countries is small, but a single enterprise has a large scale and a high degree of specialization, and has strong advantages in capital, technology, and customer resources.
According to the “State of the Industry Report and Research & Development” released by NADCA in October 2013, in 2012, my country was the world’s largest producer of die castings, accounting for 34% of the world’s total output.
(2) Overview of the domestic market
With the gradual accumulation of downstream manufacturing industries in China, my country’s die-casting industry has also developed by leaps and bounds with the improvement of China’s overall industrialization level, and has gradually developed into the world’s largest die-casting country. From the perspective of the output of die-casting parts, with the continuous and rapid development of my country’s automobile, communication infrastructure, 3C products, equipment manufacturing, home appliances, electromechanical instruments, light industry and other industries, as well as the transfer of foreign die-casting industries to China, die casting china industry has entered a new normal of steady growth.
As more and more high-end manufacturing industries transfer their production capacity to China, China’s die-casting industry is also continuing to upgrade its structure in the process of growth, and the proportion of precision die-casting parts is gradually increasing. As of the end of 2013, the proportion of China’s die-casting products used in the automotive industry has exceeded 70%, which is basically the same as that of developed countries.
As the most important category of products in the die-casting industry, the demand for auto parts, especially aluminum alloy die-casting parts for automobiles, will largely affect the overall development prospects of the die-casting industry. From the perspective of the structure of the whole car, in addition to the large number of precision die-casting parts used in the automobile engine, gearbox, transmission system, steering system, and electronic control system, aluminum alloy die-casting parts have also been used for large components such as the body frame.
Market overview of automotive die casting industry
As the most important application field of die-casting products, a large number of precision die casting parts are used in automobile engines, gearboxes, transmission systems, steering systems, and electronic control systems. The demand for auto parts will greatly affect the overall development of the die-casting industry. prospect.
As people pay more and more attention to automobile energy saving and environmental protection, the automobile industry has shown a trend of replacing steel and iron with aluminum in the past three decades, and this trend is still continuing. At present, the global aluminum alloy die casting market for automobiles is showing a rapid development trend as a whole.
In addition, in addition to aluminum alloy die castings, zinc alloy, magnesium alloy and copper alloy die castings are also used in automobiles.
The demand for aluminum, zinc and other metal die castings in the automotive industry will continue to grow in the future, which is mainly affected by the following factors:
China’s auto industry will maintain a relatively fast development speed
Since the reform and opening up, with the rapid growth of my country’s economy, the automobile die casting industry has also achieved rapid development. In 1980, my country’s automobile production was 222,300 units, and by 2016, it increased to 28,120,000 units, an increase of 125.49 times. In recent years, affected by the international and domestic economic situation, the growth rate of my country’s automobile production has declined, but due to the high base, the annual new automobile production is still quite large.
In 2016, my country’s private car ownership was 146 million, with 36 cars per 100 households, far below the level of developed countries. Therefore, china auto industry still has a lot of room for development in the future.
The trend of lightweight automobiles
The so-called lightweight of the car is to reduce the curb weight of the car as much as possible on the premise of ensuring the strength and safety performance of the car, thereby improving the power of the car, reducing fuel consumption and reducing exhaust pollution. For the lightweight of the whole vehicle, different components can contribute to different degrees. The lightweight of the body, interior and exterior trim, and power system is of great significance for reducing energy consumption during vehicle driving. Aluminum alloy materials are lightweight, recyclable and easy to form. Theoretically, an aluminum car can reduce the weight by 30%-40% compared with a steel car, among which the aluminum engine can reduce the weight by 30%, the aluminum radiator is 20%-40% lighter than the copper one, and the all-aluminum body is 40% lighter than the steel one. % or more, the weight of automobile aluminum wheels can be reduced by 30%. Therefore, aluminum alloy material is one of the most ideal materials for automobile lightweight.
Since 2011, due to the consideration of reducing greenhouse gas emissions and reducing the dependence on fossil energy, the indicators of automobile fuel consumption have been continuously improved. As one of the key technologies for vehicle energy saving, light weight has a significant energy saving effect. A 10% weight reduction for gasoline passenger vehicles can reduce fuel consumption by 3.3%, and a 15% weight reduction can reduce fuel consumption by 5%; for diesel passenger vehicles, fuel consumption can be reduced by 3.9% and 5.9% respectively.
Lightweight also has a good energy saving effect on electric vehicles (including plug-in hybrids). Weight reduction of 10% and 15% can achieve 6.3% and 9.5% of power consumption, respectively. The researchers also conducted related experiments on trucks of different energy categories, and also showed good energy-saving effects.
Reducing the weight of the car can reduce the engine load, improve the driving performance of the car, effectively reduce the braking distance, and make the steering and cornering process more flexible, thus making the car more stable, and the aluminum alloy structure can absorb and disperse more energy when it is impacted. , thus more comfortable and safe. Affected by this, the penetration rate of aluminum used in various major components of automobiles will increase significantly in the next decade. According to Ducker Worldwide, the penetration rate of aluminum hoods will increase from 48% in 2015 to 85% in 2025, and the penetration rate of aluminum doors will increase from 6% in 2015 to 46% in 2025. Specifically reflected in the average aluminum consumption per bicycle, the average aluminum consumption per vehicle in North America was 54kg in 1980, and increased to 154kg in 2010. It is expected that the average aluminum consumption per vehicle will reach nearly 325kg by 2025.
(3) The development of new energy vehicles will further promote the demand for metal die castings
One of the main problems of current new energy vehicles is the short cruising range, and lightweight design has become the main measure for reducing weight and consumption of new energy vehicles. Taking Tesla (TESLA) Model S as an example, its total weight is 2,108kg, and the weight of the battery alone exceeds 500kg. In addition, the drive motor increases the weight of the whole vehicle; while the total weight of the engine of a traditional car is generally 80-160kg. The mileage of a 70L gasoline car can reach 700-900Km, while the cruising range of an electric vehicle with a 500kg battery is only about 400Km. Therefore, increasing the proportion of automotive aluminum alloy die castings is the main measure to reduce the weight of new energy vehicles.
With the release and implementation of my country’s automobile energy saving and emission reduction policies, my country’s new energy vehicles have shown a rapid development trend in recent years. In 2016, the cumulative production of new energy vehicles was 517,000, an increase of 49.99% over 2015. Among them, the output of pure electric passenger vehicles increased most significantly, up 73.10% compared with 2015; the production of pure electric commercial vehicles increased by 50.20% compared with 2015; the output of plug-in hybrid electric passenger vehicles increased by 29.9% compared with 2015. From January to June 2017, the cumulative production of new energy vehicles was 212,000, an increase of 19.77% over the same period of the previous year. Among them, the output of pure electric passenger vehicles increased most significantly, up 30.60% over the same period of the previous year.
New energy vehicles have stricter requirements on body weight than traditional energy vehicles, so more lightweight aluminum alloy die-casting parts are used. For example, 95% of the Tesla (TESLA) Model S series models use aluminum alloy materials. The sustained and rapid growth of new energy vehicles will form a strong impetus for the development of the automotive aluminum alloy die casting industry.
What Is Die Casting – Die Casting Method
What Is Die Casting – Die Casting Method
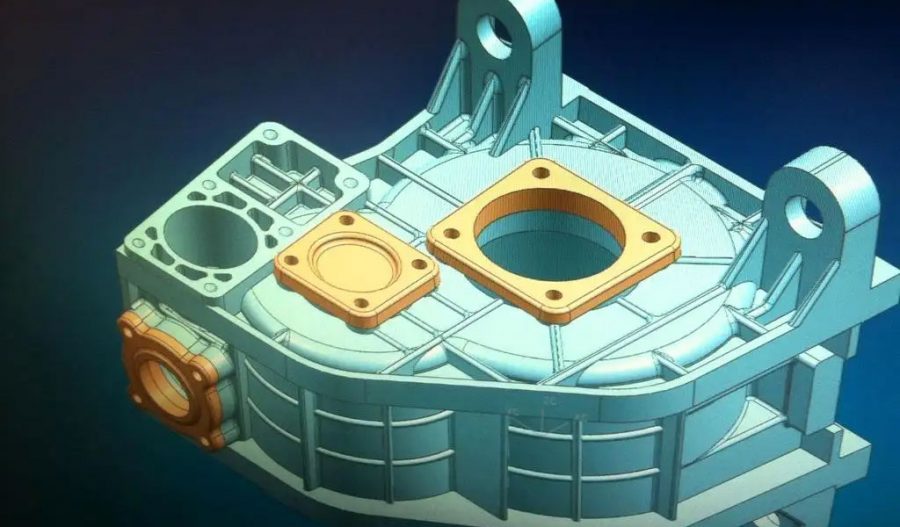
What Is Die Casting?Die Casting and it is a precision casting method that obtains the same casting as the mold by injecting molten metal into a steel mold that is precisely machined to perfectly match the required casting shape. In addition to the advantages of almost no need for finishing as the dimensions are accurate, it has excellent mechanical properties and is capable of mass production.Die casting is also called pressure die casting. It is a precision casting method in which molten metal is injected into a steel mold that is precisely machined to perfectly match the required casting shape to obtain a casting identical to that of the mold. The product is called die-casting parts.
In addition to the advantage that there is little need for finishing because the dimensions are accurate, it has excellent mechanical properties and can be mass-produced. The metal used is an alloy such as zinc, aluminum, tin, copper, and magnesium, and it is cooled and solidified by injecting it by air pressure, water pressure, or hydraulic pressure using a die-casting machine.
There are many automobile parts as products, including parts for electrical equipment, optical equipment, vehicles, weaving equipment, construction equipment, and measuring instruments.
The Definition And Terminology Of Die Casting
Die casting is defined as “a casting method that mass-produces castings with excellent casting surfaces with high precision by pouring molten metal into a precision mold and products resulting from it”. In Japanese, the word “die casting” is also used, but American die casting is adopted. In the UK, mold casting is called gravity die casting, low pressure casting is called low pressure die casting, and die casting is called pressure die casting.
The Characteristics Of Die Casting
The main advantages and disadvantages of die casting are as follows.
“Advantages”
- Products with complex shapes can be mass-produced in one process.
- Because it is high-speed and high-pressure filling, there is no molten metal vortex and the dimensional accuracy of the casting state is good.
- Because it is a high-speed and high-pressure filling, the hot water flow is good, a thin product can be made, and the casting surface is beautiful.
- The productivity per hour is good because it is fast charging and rapid cooling and solidification.
- Mechanical properties are improved by the formation of a seven-layer by rapid cooling.
“Disadvantage”
- Coping with pores caused by the inflow of air or gas.
- Solution treatment or welding cannot be performed due to the inflow of air or gas.
- Since the mold is expensive, economical mass production cannot be secured.
Die Casting Machine
Because the sleeve and flanger are not in the molten metal and are not heated, it is called a gold chamber.On the other hand, a machine called a hot chamber is used for die casting of zinc or magnesium and is not used for aluminum alloy. Cold chamber die casting machines in Japan have a minimum clamping force of 0.5MN and a maximum of 40MN. The injection force is 1/10 to 10/20 of the clamp force.
Die Casting Cycle
One cycle of aluminum alloy die casting by cold chamber machine will be described.
- a) Close the two molds by matching the movable mold to the fixed mold by the machine’s mold clamping operation. With a ladle, molten aluminum alloy is poured into a sleeve called a cold chamber.
- b) The plunger operates and presses the molten metal into the mold cavity at high speed and high pressure. The mold is water cooled to prevent overheating.
- c) When the molten metal solidifies, open the mold and return the flanger and the moving core to their original state.
- d) Operate the extrusion pin to push the product out of the die casting molds.
The size of the machine used depends on the size of the die-casting product. One cycle of die casting takes several seconds for small size and several minutes for large size. In recent die casting production, some factories are aiming to automate their operations and unmanned them.
Casting pressure, which is a typical casting condition item of aluminum die casting, is in the range of 10 to 200 MPa, and the gate speed is in the range of 2 to 100 m/s. The casting conditions of die casting are quite different from those of gravity casting.
Features are as follows
- Cast with high pressure
- Cast at high speed. Therefore, the filling time into the mold is very short
- In the mold, the filled molten metal is rapidly cooled and solidified.
Die Casting Manufacturing Process
Die casting work performed in most factories is supported by automatic hot water supply device, plunger lubrication device, automatic spraying device, product dispensing device, etc., and is being mechanized and systemized. Fully automatic operation and unmanned operation are also being realized. The trimming device mainly relies on the knitting press operation, but sand blasting or shot blasting are also used in combination. In post-processing, machining and surface treatment are performed. For the surface treatment, buffing, chemical conversion, painting, anodizing, plating, and the like can be selected.
Dimensional Tolerance Of Die Casting
It goes without saying that the dimensional accuracy required for a product is after final processing, and errors in material and processing are added.
The dimensional tolerance of the typical aluminum alloy die-casting ADC12 in the as-cast state can be interpreted as follows.
- Dimensional tolerance = casting tolerance + mold tolerance + shrinkage vs. calculation tolerance + tolerance for casting operation
- Calculation formula for maximum possible dimensional tolerance – ε=±0.75×10-³×L。(mm)
- Calculation formula for precise dimension tolerance – ε=±(1.15×10-³×L。+0.1) (mm)
- Calculation formula for general dimensional tolerance – ε=±(2.15×10-³×L。+0.2) (mm)
In this case, L. is the length of the mold cavity at room temperature, and ε is the dimensional difference of the die casting. The factor that fluctuates the casting tolerance is the mold temperature difference.As a standard for dimensional tolerance, there is JIS B 0409 die casting normal tolerance, and the normal tolerance of length and the maximum value of degradation angle are determined.Japan Die Casting Association standardized the details again and indicated length tolerance, angle tolerance, flatness tolerance, and eccentricity tolerance.
The Mechanical Properties Of Die Casting
The mechanical properties of die casting show the measured values of the simple shape individual molten metal injection test pieces and the measured values of the test pieces cut from mass-produced products. In general, the former is larger than the latter. ASTM test pieces are distributed as individual molten metal injection test pieces.
The strength of die casting cannot be guaranteed as a substitute characteristic. Apply a load corresponding to the actual and practical load to the die casting to destroy it, and obtain a numerical value that can be statistically guaranteed to withstand the load, for example, the lower limit of 3σ.
Die Casting Defects And Countermeasures
The extent to which defects are allowed depends on the required quality of the product, so the limit should be clearly defined when trading.
(G) Japan Die Casting Association has suggested casting surface standards and foam standards. There is also a new defect name called Fracture Layer. It is explained that the solidified layer generated in the injection sleeve of die casting is an abnormal tissue that is broken by the flanger and flows into the molten metal into the cavity. The strength of the interface between the fractured layer and the normal tissue is significantly lower than the strength of the normal tissue as it is inserted at less than 9kgf/mm². This is the cause of extremely lowering the strength of the die casting. According to the degree of demand for the strength of die casting, the development of a method for preventing the occurrence of a fracture layer is in progress. Methods to increase the heat retention of the molten metal in the sleeve just before injection, such as the ceramic sleeve method and the powder lubrication method, are being sought.
New Die Casting Method
Die casting has been quantitatively expanded by using high productivity and good flow of hot water for thin products as sales points. However, the high-speed charging that realizes it, on the one hand, cannot avoid air bubbles due to mixing.
may be the cause Several new die casting methods have been developed in response to product design requirements such as filling, airtightness, and strength leveling as castings, and heat treatment or welding.
(1) Vacuum Method
The history of vacuum method is quite old. Methods currently industrially known include the GF method, the mass vent method, the shutter-off pin method, the RSV method, the superback method, the MFT method, and the VACURAL method. The vacuum method widely used in Japan is the GF method.
(2) PF Method
Also called non-porous die casting. The principle is to eliminate air bubbles by purging the mold cavity and sleeve with oxygen, mixing oxygen with the molten metal in the spray state by high-speed injection, and fixing oxygen with Al₂O₃. Die casting made by PF method can be solution heat treated and artificial aging heat treated. Sometimes welding.
(3) Local Pressure Method
After filling the mold cavity with the molten metal, a local pressure higher than the casting pressure is applied to the molten metal or the reaction solid in the cavity by pressing a pressure pin by a predetermined stroke. There is an effect of filling the voids of the decrease in the cavity volume caused by such pressurization. It is effective as a countermeasure against air bubbles in the thick part isolated in the part away from the gate.
(4) Hot Chamber Method
The hot chamber machine method is named because the injection mechanism is immersed in the molten metal. Since the steel injection mechanism part is easily eroded by the molten aluminum alloy, a hot chamber machine is usually not used for aluminum alloy die casting. However, if this method can be applied with high productivity, high level of automation, and stability of molten metal quality, new demand development can be expected for aluminum alloy die casting. In 1987, the Small and Medium Business Corporation tested a hot chamber die casting machine with a clamping force of 2.5MN. Ceramic materials such as silicon nitride are used for parts in contact with molten aluminum alloy. As a result of the operation test, improvement in quality, slimming, productivity improvement, and energy saving can be expected.
(5) Collapsible Core Method
One of the disadvantages of die casting is the restriction on the undercut shape. One of the solutions is to use a metal neutralizer setting. Another method, which is a collapsible reactor, uses salt or silica sand as an aggregate.
The Development Of Die Casting
The global aluminum die-casting market is expected to show continuous growth in accordance with the trend toward lighter weight of parts used in the automotive and aerospace fields.
Grand View Research’s ‘Global Aluminum Die Casting Market’ report that contains such content forecasts that it will grow at a CAGR of 5.1% from 2021 to 2028, reaching $35.64 billion in 2028.
Aluminum die casting is a process of injecting molten aluminum by applying pressure to a mold, and is divided into pressure die casting and other processes depending on the production process.
According to the report, high pressure die casting manufacturer (HPDC) in the production process sector accounted for the largest revenue share in 2020 and this trend is expected to continue through 2028. This is explained by the high preference for HPDC among casting manufacturers due to the high efficiency of the process.
It also points out that increasing demand for aluminum die casting or zinc die casting products is intensifying competition in the market, leading market players to gain a competitive edge through strategic initiatives such as mergers and acquisitions (M&A) and increased production capacity and to gain a competitive edge in losses from the impact of COVID-19. expected to recover.